Waste creation begins when raw materials get manufactured into building materials. Let’s follow the trajectory of a standard 2x4 piece wood stud from it’s initial harvesting from a tree down to it’s end of life.
Trees get chopped down as raw material.
Wood pieces get sent to a lumber mill.
Wood gets processed into standard sizes.
Wood gets treated.
Wood gets sent to the lumber yard and gets purchased by builder.
Builder cuts down wood to appropriate size for the design.
Excess wood gets tossed, recycled, or used elsewhere on site.
During a future renovation, wood stud either remains or gets demolished.
Nails and toxic finishes gets removed.
Old studs get sent to a lumber mill and recycled into wood chips.
Wood chips get used for mulch, flooring, or burning.
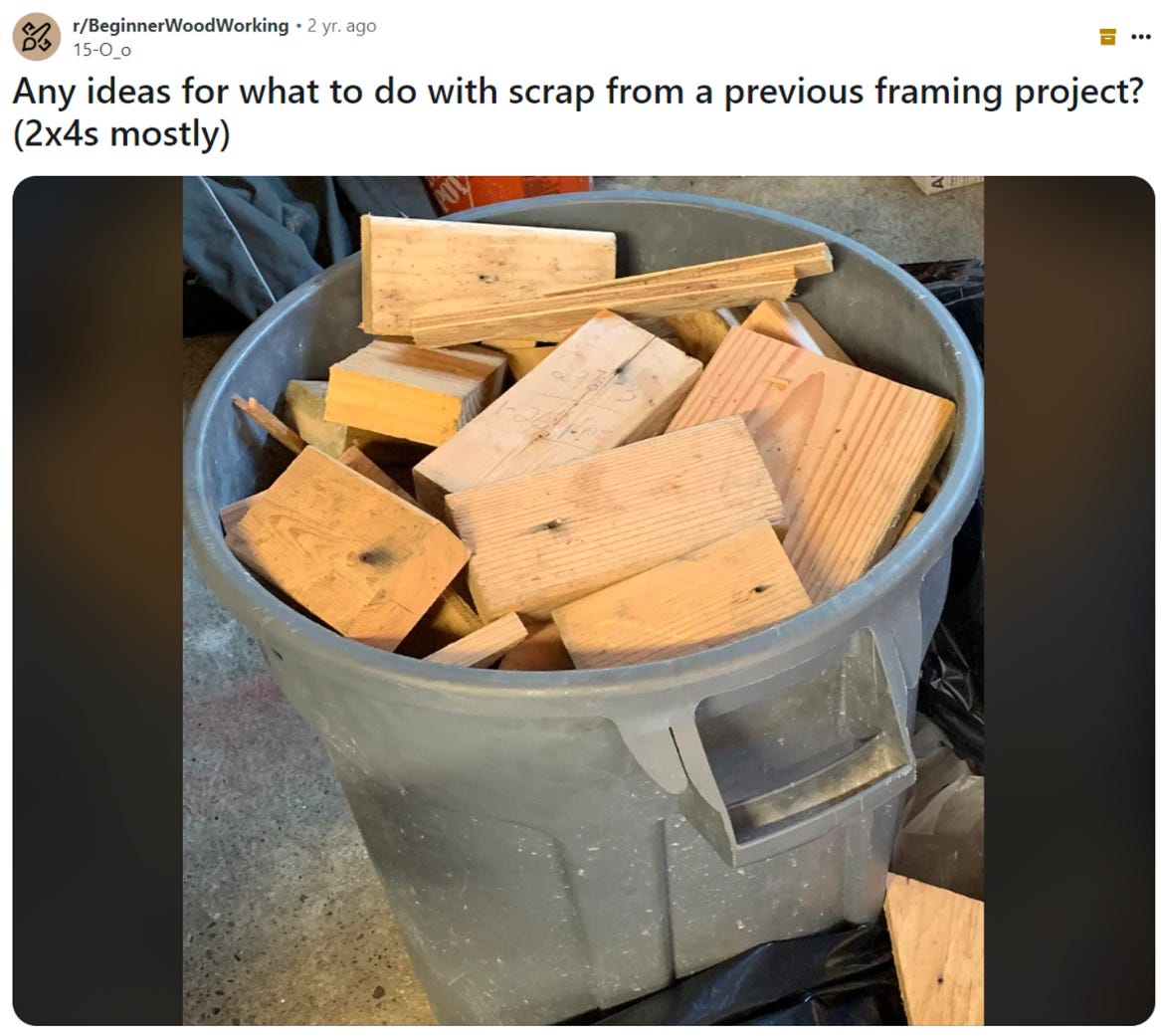
This is one example of one material’s waste stream. Every material goes through it’s own waste journey. During the design and planning phase, you aren’t manufacturing, installing, or demolishing the product. You are specifying and quantifying it. This means you can prescribe what material and how much of it goes into your building (whether or not the builder chooses a substitute is a different story, though!)
Specifying Materials that Last
During the early phases of design, architects & engineer work with owners to define the building structure, exterior and interior materials, and overall aesthetic. It’s unlikely that everything gets specified at this stage. However, the design team and the owner can dictate specific materials builders should use (it’s often stronger if the requests live in contractual documents). Tips to minimize waste include:
Sourcing sustainable materials from reputable vendors
This may cost more upfront, but high-quality materials last longer and will require less maintenance, thereby reducing the risk to spend money maintaining or replacing later on.
Conduct your due diligence before selecting a product. Understand it’s life cycle, degradation process, and operating costs over time. The owner will want to know these things, too!
Incorporating recycled material into your specifications
Use reclaimed wood, or recycled products, like TimberHP, in your design. There’s a chance that the same materials is recyclable later on, too.
Use services like Material Bank during sample selection
Designers love samples, but not all of them will get used and go to waste. Use services like Material Bank during the sample selection process to ship unused materials back.
Quantifying Materials
Waste during construction can come in the form of an excess of unwanted materials. Generating material take offs from a Building Information Model (BIM) file can get you an estimate of the materials required. The rise of BIM enables teams to quantify building materials before construction even begins.
The pre-requisite requirement is an accurate BIM file. Even if it’s not 100% accurate and contains all the nuts and bolts (rarely you’ll include this level of detail anyway), people can still generate rough estimates from the model. This will give the builder a rough order of magnitude.
Not only that, it’ll save the construction team time from having to estimate quantities themselves.
If you’re using a BIM tool like Revit, you can easily export a bill of materials straight from the schedules.
Now, there is software like like Higharc, that will output the take-offs from your standard designs for you.
Alternative Methods of Construction
Most buildings in the world are still constructed on-site using “traditional” methods. The rise of off-site construction or alternative methods of building aim to streamline the build process and reduce waste. These include:
3D print your structure
This new building process is operationally intensive, expensive, and in theory, reduces waste. You’re printing exactly what the model prescribes and nothing more. Companies like ICON 3D and Mighty Buildings have completed dozens of 3D printed homes across the nation.
Pre-fabricate parts or the whole thing
Pre-fabricating components, like cabinetwork, or entire buildings, like accessory dwelling units, off-site can significantly reduce waste. The factory contains all of the work and labor. Objects like these are inherently pre-planned and engineered to precision to minimize waste during production. Repeatability allows standard components and processes to come together and produce at scale.
Companies like Volumetric Building Companies and Abodu spent years refining their build processes to minimize on-site construction time.
Planning is one thing…going into active construction is another
Like with many things in construction, all of this is easier said than done. Stronger outcomes are more likely when architects, engineers, and consultants work closely and collaboratively with builders to achieve the desired results. We all know that gaps in information and communication can tarnish the process and not only lead to a waste of materials, but also a waste of time. But we’re hopeful that sustainable materials, BIM technology, and off-site construction are ways to save mass amounts of stuff from going to landfill.